- MINEM: Estudiantes de Cajamarca fueron instruidos en actividades de remediación ambiental y exploración minera
- China declara que “ignorará” los “juegos de números arancelarios” de EE.UU.
- Beca PERUMIN: Más de 2180 jóvenes de 23 regiones del Perú postularon para acceder a las actividades de la Convención Minera
- Minem: el Algarrobo es el primer proyecto en priorizar el recurso hídrico en Perú
- MINEM: Cusco será la primera región del país con proyectos en energía rural trifásica
Tecnología e innovación en plantas concentradoras
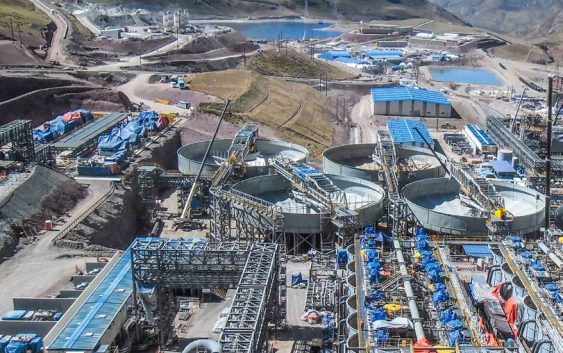
La industria de plantas concentradoras ha tomado un enfoque altamente tecnológico, basada en la digitalización y automatización. Las empresas mineras caminan hacia la excelencia operacional y el siguiente paso sería incorporar el internet de las cosas.
En ediciones anteriores, hemos desarrollado algunos de los conceptos que giran alrededor de una planta concentradora, tales como su compromiso a minimizar el consumo de energía, reducir el empleo de recurso natural del agua y minimizar sus emisiones de carbono a través del diseño e implementación de circuitos de conminucion, entre otros aspectos.
Hoy, a este escenario se suma un elemento contundente y determinante: La tecnología. Si bien esta ha estado siempre presente, en la actualidad su presencia dejó de ser una opción para convertirse en una necesidad. Basada en la digitalización, la automatización y la innovación, la tecnología se ha constituido en el eje indispensable para el óptimo funcionamiento de las plantas concentradoras.
CHINALCO
Eduardo Ku, vicepresidente de Operaciones Mina de Minera Chinalco, comenta que “las plantas concentradoras no son una isla en el mundo de la tecnología. La tecnología avanza y el uso de celulares y los wireless también. Hay instrumentos que ya no requieren cableado y el uso de plataformas digitales se están usando en las plantas cada vez más, agresivamente y con mayor confianza.
Ejecutivo de Minera Chinalco comenta que en este momento, el trabajo de la planta concentradora es seguir avanzando en conseguir incrementos en el throughput, mejoras en la recuperación, mejoras
en la ley utilizando lo que significa la instrumentación y el control, siempre optimizándolos y con las mejoras que propiamente se da día a día con la ayuda de los equipos de trabajo, con los operadores, etc. A nivel de instrumentación y control, la operación minera tiene una diversidad de equipos e instrumentos desde la planta de chancado hasta la planta concentradora, cuentan con cerca de 20,000 entradas y salidas, más de 4 mil instrumentos que es necesario mantenerlos adecuadamente para que estos equipos funcionen apropiadamente, priorizando la seguridad del operador.
En cuanto a los sistemas y/o tecnologías que están empleando, Ku detalla que emplean la tecnología de sistema de control distribuido, “que en nuestra planta es a través de la plataforma ABB”. Adicionalmente, cuentan con una infraestructura técnica de fibra óptica que abarca todas las zonas de operación, usando gran número de videocámaras y plataformas digitales, así como cables de fibra óptica. “En general la planta está bien automatizada”.
EL BROCAL
En el caso de Sociedad Minera El Brocal, la situación es relativamente distinta, pues está atravesando una etapa de transformación y dentro de esa transformación se incluyen algunos cambios importantes que están dándose a nivel de control de procesos.
Joe Pezo, gerente de Procesos Metalúrgicos de Sociedad Minera El Brocal, comenta que una de las cosas que están ambicionando es que al terminar este año, logren integrar la plataforma de controladores que tienen en la planta concentradora número 2, que es la planta de plomo – zinc.
El ejecutivo indicó que una de los aspectos que ya se realizaron es justamente la integración de los controladores del circuito de fajas de la planta de chancado y lavado. Comentó que en el 2014 concluyeron un proyecto que implicaba utilizar una filosofía que inicialmente estuvo concebida y trabajada con controladores y procesadores ABB, pero por restricciones de presupuesto no se llegó a culminar.
“En este año, justamente estamos retomando este tema, para terminar de integrar todos los controladores que tenemos en planta, para que una vez integrados, podamos hacer un mejor control de las variables del proceso”, explicó. Pezo comentó que también han adquirido el software PIA, un software de control de procesos que permite centralizar toda esta información y a través de gráficas de control monitorear y evaluar variables importantes del proceso, para tomar las decisiones más apropiadas.
Cabe precisar que El Brocal cuenta con dos plantas concentradoras. “La Planta 1, que procesa cobre es una planta antigua que nos proporciona aproximadamente unas 7,000 toneladas por día, estamos en un proceso de upgrade de esta planta, que nos va a permitir incrementar de 7,000 toneladas a 10,000 toneladas por día”. En tanto, la Planta 2 procesa alrededor de 14,000 a 15,000 toneladas por día de plomo y zinc.
Para el gerente de Procesos Metalúrgicos de Sociedad Minera El Brocal, los procesos de automatización, a veces, son un poco complicados de justificar, desde el punto de vista económico, porque se basa inicialmente en supuestos. “Como no hay una información histórica y todos los procesos no son iguales, no se puede utilizar a priori lo que ocurrirá en una planta “X”. Eso no se puede hacer. Lo que sí hacemos es basado en las mejoras que podamos obtener, estimar un beneficio económico que potencialmente, inclusive, puede ser mayor”, agrega.
LAS BAMBAS
En el caso de Minera Las Bambas, Julio Palomino Calle, superintendente de Control de Procesos de la citada compañía, comenta que de acuerdo a su plan estratégico están optimizando sus operaciones, tanto desde la parte de minado como de los procesos que tienen en la planta.
“Tenemos implementado tecnología de última generación, controlamos correctamente nuestro rendimiento y nuestra disponibilidad de los equipos en tiempo real”, anotó. Añade que prácticamente la tecnología que se ha implementado en la unidad minera Las Bambas, permite monitorear y saber si es que tienen que tomar acción en alguna etapa del proceso para optimizar su rendimiento y eficiencia.
En el área de Control Automático han implementado sistemas de control avanzado en las etapas de molienda y espesamiento. Del mismo modo, en el manejo de la información, disponen de soluciones que les ha permitido hacer monitoreos en tiempo real. “Nuestros estándares son corporativos de MMG (estatal china propietaria de Minera Las Bambas) y nos permite estar en el camino hacia la excelencia operacional”, mencionó.
Julio Palomino refirió que la tecnología actual, a nivel de plantas concentradoras, está bastante implementada.
“Si hablamos de cobre, en comparación a otros países alrededor del mundo, estamos prácticamente al mismo nivel. Hemos implementado en Perú la última tecnología disponible. Me refiero a temas de información, monitoreo en tiempo real y estrategia operacional”, reveló. El especialista opina que en los últimos 20 años no solo se ha dado un boom económico, sino también un boom tecnológico. “Nuestros profesionales se han visto involucrados en nuevas tecnologías, lo cual exige que los profesionales que trabajamos en minería, nos sintamos motivados a estar al día con las tecnologías disponibles”, concluye Palomino.
LAGUNAS NORTE
En Barrick se está manejando a la digitalización y a la innovación como una nueva cultura corporativa de la compañía. Así lo afirma Leoncio Chávez, jefe de Control de Procesos de Lagunas Norte, quien refiere que buscan tener ese pensamiento de empresa digital.
Precisamente, en Lagunas Norte se viene trabajando el proyecto denominado “Gestión de producción de oro en tiempo real y digitalización de los procesos”. Chávez detalla que han escuchado diferentes formas de optimizar los procesos a través de lazos de control.
Los lazos de control, en realidad, no tienen propiedad, por más que puedan tener diferente marca y fabricante. “Quien hace o define que estos lazos de control sean realmente estratégicos para optimizar el proceso, son quienes están involucrados en esta mejora, personal de metalurgia, de control de procesos y de operaciones que tiene el expertise. Es la conjunción de diferentes conocimientos y estrategias para que ese lazo de control funcione”, explica el especialista.
Pero el lazo de control no solo es un componente tecnológico que usa la planta. Cuando se hace una revisión de toda la tecnología que se tiene en una planta, aparecen diferentes tecnologías en diferentes niveles de gestión, y los lazos de control están incluidos dentro de los procesos de la planta, pero también hay diversas tecnologías que la soportan.
Justamente, este proyecto se trata de cómo la tecnología que se tiene en el proceso, la administras y la alineas para que los gerentes encuentren en esta tecnología un valor agregado a la toma de decisiones.
“Este proyecto consta de cuatro niveles. El primero es la Instrumentación. “¿En una planta procesadora de dónde sacamos el dato? En el proceso. El proceso es el que nos da la información. Mientras que una empresa comercial se basa en clientes, una minera saca información de los procesos Hay millones de datos que si son transformados y organizados, nos dan un valor agregado a la información”, expresa Leoncio Chávez.
El primer nivel se trata de eso, cómo recopilar la información, ¿a través de qué? a través de instrumentos (un sensor o nivel, una balanza, un motor, etc.). Esto brinda datos, tales como amperio, toneladas por hora, porcentajes, etc. El segundo nivel se da cuando esos datos son transformados en información, y se comienza a controlar la planta.
“Por ejemplo, si determinas que hay una desviación y una anomalía en el control, empiezas a tomar acciones, a nivel de equipos, de operarios y de todo el recurso que se necesita para controlar una planta concentradora”, explica.
El tercer nivel habla de un nivel de integración, que puede indicar que este control tiene que “conversar con ciertos planes”. Se trata de cómo hacer para que esa tecnología que un operario controla, se integre con la tecnología que define o planifica la producción.
“Aquí, integras sistemas e información, para que, en el cuarto nivel, los gerentes puedan tomar las decisiones del caso, pero teniendo la información determinante del proceso. Nació del nivel 1, de un instrumento que prácticamente monitorea el proceso”, detalla.
Este proyecto empezó en el 2016, a nivel corporativo. La casa matriz realizó la optimización de procesos y ha visto conveniente que dentro del triángulo: negocio, estrategia y tecnología, la empresa tendrá una ventaja comparativa a nivel de mercado. “Lo que estamos haciendo en Lagunas Norte es recoger esas buenas prácticas e implementarlas dentro de nuestra mina”. Por ejemplo, para el caso de un proyecto de ahorro de dosificación de cal, se está pronosticando que en el 2017 se registre un ahorro de US$ 1.2 millones (solo en Lagunas Norte, porque a nivel de Barrick se están haciendo muchos otros proyectos bajo el concepto de digitalización).
Leoncio Chávez asegura que solo alineando la tecnología y haciendo convergencias de sistemas, la tecnología se vuelve en un pilar dentro de la arquitectura tecnológica para lograr resultados importantes.
PERSPECTIVAS
Sobre cómo observa el panorama de plantas concentradoras en los próximos años, Joe Pezo, gerente de Procesos Metalúrgicos de Sociedad Minera El Brocal, dijo que vislumbra un futuro bastante bueno.
“He trabajado en plantas concentradoras en los años 1998 y 1999, en donde el nivel de automatización, las centralizaciones de los controladores eran bastante básicos. Han pasado casi 20 años y veo una mejora sustancial en lo que son sistemas de control para circuitos de molienda y flotación”, opina. Considera que el cambio es radical. “Ahora, se emplean estos sistemas justamente para hacer eficiente los procesos y el siguiente paso es comenzar a incorporar el internet de las cosas. Eso va a permitir al área de Procesos comenzar a recopilar información que va a ser útil para la interpretación y definir de manera anticipada probables problemas que puedan ocurrir en el proceso”.
“En la medida que tengamos mayor información en tiempo real de los principales parámetros del proceso a partir de instrumentos que puedan generar esa información y estadística directamente, eso va a tener un impacto fuerte en la toma de decisiones en el ahorro del costo operativo”, agrega Pezo.
Esto, dado que, al tener mayor información sobre el estado de un determinado equipo, el mantenimiento predictivo preventivo mejorará sustancialmente y los tiempos de la corrección de los problemas evitarán futuras paradas cortas o largas en el proceso. “Eso se está viendo ya, quizá no en la magnitud que debería ser, pero creo que poco a poco las gerencias generales están comenzando a entender y adoptar este tipo de mejoras en beneficio de las plantas de procesamiento”, señala.
A su turno, Eduardo Ku, vicepresidente de Operaciones Mina de Minera Chinalco revela que ya cuentan con aplicaciones de wifi de WiMax, a través del cual el operador camina con su ipad y hace control sobre los equipos, completamente inalámbrico. “El futuro de toda planta será la automatización y la digitalización de los procesos en forma permanente”. En Chinalco, por ejemplo, esto ya se está viendo. “Hay mucho trabajo de automatización a nivel de los procesos de gestión. Mucho uso de tecnología para el control de procesos. Es como traer el futuro a Chinalco”, destacó.