- Ingemmet busca culminar la revisión de 4 mil expedientes de petitorios mineros a inicios de 2026
- Chirif: Ingemmet analizará distribución geográfica y situación de Reinfos en el proceso de formalización minera
- Predictiva y eficiente: así funciona la IA en la planta de procesos en Quellaveco
- Especialistas concuerdan que la criminalidad es el principal factor que enfrenta la minería y la sociedad en general
- FMI destaca “fuerte recuperación” de la economía peruana
Mineras destinan hasta 15% de la inversión de la operación en mantenimiento
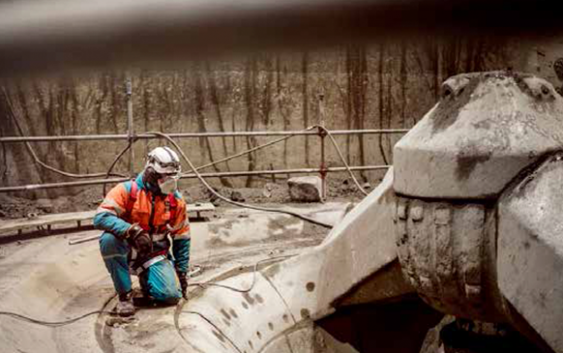
Para que los equipos estén en óptimas condiciones en una operación minera, Maykol Valdez, Mining, Crushing & Screening Manager Metso, sugiere que el mantenimiento se realice de manera predictiva para pronosticar fallas futuras en los equipos e intervenirlos adecuadamente en paradas programadas.
¿Qué aspectos se deben considerar para que los equipos estén en constante mantenimiento y óptimas condiciones en una operación minera?
El mantenimiento es una práctica importante y crítica dentro de la industria minera porque permite que los equipos trabajen adecuadamente y de forma segura, lo que conlleva a que la producción vaya al ritmo de lo planificado y se obtenga las ganancias de acuerdo a los objetivos de la empresa.
Por lo general, las empresas mineras, dependiendo de la magnitud de la producción de la mina, invierten aproximadamente entre un 12 y 15% de la inversión total de la mina.
Este monto se destina para todos los tipos de mantenimiento que se realiza a una máquina a fin de que siempre esté operativa. Lo ideal es realizar el mantenimiento de manera predictiva para pronosticar fallas futuras en los equipos e intervenirlos adecuadamente en paradas programadas y no hacerlo de manera intempestivas que ocasionan pérdidas en la producción.
Las empresas mineras deben tener todo lo necesario para ejecutar un mantenimiento en el momento oportuno, para lograrlo se debe contar con un stock de repuestos, personas calificadas y una supervisión adecuada.
¿Cuál es el desafío para Metso?
Parte de nuestros desafíos es asegurar la mayor utilización del equipo a través de repuestos originales, sin sacrificar su duración; y ser un socio estratégico para anticiparnos a las necesidades del cliente de manera inmediata, y no generar retrasos en los mantenimientos o en las paradas programadas.
“La diferencia entre Perú y otros países, con respecto al mantenimiento de los equipos, se basa en la cultura”.
La mayoría de las empresas mineras cuentan con cierto stock en su planta, empero planifican un consumo que en realidad no abastece, es ahí donde los proveedores tienen que mantener un stock por encima de lo recomendado para cubrir con la emergencia. Por eso, es importante trabajar con un OEM, Original Equipment Manufacturer, (fabricante original), porque no solo vendemos los repuestos y hacemos servicios, sino que también realizamos el cuidado posterior del equipo para sacarle el mayor rendimiento. Y eso es algo que nosotrosllamamos TCO (Total Cost of Ownership), es decir que realizas un gasto mayor a primera instancia, pero en tu análisis final tienes un ahorro considerable.
Entre los equipos que tienen mayor recurrencia al mantenimiento están las fajas transportadoras porque sus componentes fallan constantemente y requieren cambios, otros quipos son las chancadoras, molinos, bombas y celdas de flotación.
¿Cómo impacta la implementación de procesos eficientes de mantenimiento en la capacidad productiva?
El costo de inversión para el mantenimiento se incrementa cada año debido a que las minas buscan elevar su producción.
Es difícil ver una mina que produzca lo mismo por más de cinco años, lo que implica mayor exigencia de los equipos, o la adquisición nuevas máquinas. Muchas plantas concentradoras ya tienen cierto grado de automatización a través de sistemas que pueden controlar parámetros y prevenir algunos mantenimientos, sin embargo, aún la incidencia en la inversión en porcentajes es mínima.
Con respecto a los tiempos, Metso utiliza una metodología que se llama SMED que consiste en hacer un análisis cronometrado de todas las actividades que involucra una parada de planta.
Hacemos el análisis, medimos, realizamos histogramas y verificamos en qué punto hay deficiencias para que, en una futura intervención, se pueda ahorrar tiempo.
Existen otras tecnologías para desarrollar mantenimientos y cambios de componentes en los equipos en menos tiempo, como por ejemplo en revestimientos de molinos, de esta manera se reduce a la mitad el tiempo del intercambio para evitar que la máquina esté parada y pueda operar la mayor cantidad de horas en el día.
En Perú, las empresas mineras, por lo general, tienen un equipo grande de mantenimiento y tercerizan trabajos puntuales, a diferencia de Chile, Colombia, Guyana y Surinam, que son países en la cual utilizan la mano de obra local, pero piden asesoramientos externos.
Estamos trabajando en el cambio de cultura de prevención en las minas. La mayoría no compra mucho stock de repuestos porque no desea invertir en corto plazo. Esto puede ser perjudicial, cuando tengan un problema y no cuenten con el stock, pues se suele gastar el triple para que el material llegue pronto.
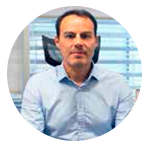