- Dynacor firma una Carta de Intenciones No Vinculante para adquirir una planta de procesamiento y activos en Ecuador
- Ingemmet busca culminar la revisión de 4 mil expedientes de petitorios mineros a inicios de 2026
- Chirif: Ingemmet analizará distribución geográfica y situación de Reinfos en el proceso de formalización minera
- Predictiva y eficiente: así funciona la IA en la planta de procesos en Quellaveco
- Especialistas concuerdan que la criminalidad es el principal factor que enfrenta la minería y la sociedad en general
Metalurgia inteligente no ferrosa
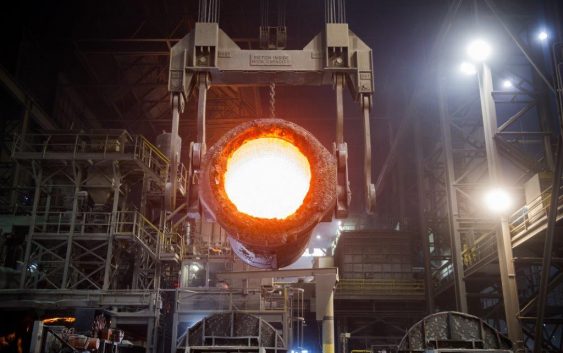
La digitalización se ha convertido en una de las herramientas de la llamada cuarta revolución industrial. Las tecnologías digitales están cambiando sorprendentemente varias esferas de nuestra vida. La digitalización también está afectando a la industria. Y naturalmente, la industria metalurgia forma parte del cambio. Tanto las funciones principales de producción como las auxiliares están siendo digitalizadas; por consiguiente, se están acumulando gran cantidad de datos sobre las mismas. Según las previsiones de la compañía Technavio, el mercado de la Inteligencia Artificial industrial crecerá a un ritmo acelerado en los próximos 3 años – un 54% anual en promedio
Las empresas dominantes en el rubro (Stena Metal International, National Aluminum company of India, Rusal, etc.) ya han intentado crear modelos basados en inteligencia artificial (IA) analizando en profundidad sus datos acumulados; y es con este fin que han creado departamentos para el análisis de datos, monetización y digitalización. Sin embargo, las soluciones basadas en IA en metalurgia no ferrosa son implementadas un poco más lentamente que en otras ramas de la industria.
¿Por qué es así y cuáles son las perspectivas de uso de la IA en la metalurgia no ferrosa?
Barreras de la digitalización
Dado el bajo contenido del componente buscado en un mineral, y las mezclas con otros elementos, la metalurgia no ferrosa tiene una estructura compleja y un proceso de producción que consume mucha energía. Por ejemplo, un mineral contiene un máximo de 5% de cobre y un máximo de 5.5% de zinc y plomo. Y la materia prima a menudo es multicomponente: puede contener alrededor de 30 o más elementos químicos. Por tanto, para producir una tonelada de cobre, se deben extraer 100 toneladas de mineral. Es así que los costos energéticos llegan a alcanzar la mitad de los costos totales relacionados con la fusión de una tonelada de metal (pueden consumirse hasta 5 kW de energía por hora para el cobre). Además, muchas ramas de la metalurgia no ferrosa también se distinguen por una conversión metalúrgica en etapas múltiples de productos intermedios. Por un lado, todos estos factores justifican el uso de tecnologías de AI, ya que estas a menudo hacen posible aumentar la eficiencia específica, que es crítica en operaciones de producción.
Por otro lado, la metalurgia no ferrosa tiene una gama relativamente amplia de productos básicamente diferentes y, en consecuencia, un espectro muy amplio de procesos de producción. Los modelos AI deben crearse teniendo en cuenta la particularidad de cada empresa metalúrgica que, incluso trabajando con el mismo metal, lo hace de manera muy diferente. Todo esto reduce el potencial de crecimiento de la solución implementada y, por lo tanto, reduce el atractivo de inversión para el continuo desarrollo de esta y aumenta los riesgos de su implementación.
“La implementación de soluciones basadas en inteligencia artificial en la metalurgia no ferrosa sea por lo general más compleja, y como consecuencia, más costosa”.
Por el contrario, en mi opinión, el proceso de implementación de AI será ligeramente más rápido en el caso de la metalurgia ferrosa. Esto se debe en parte al hecho de que los procesos de producción en dicha rama son lo suficientemente similares en las empresas de diferentes partes el mundo. Y, además, las empresas utilizan equipos de los mismos fabricantes; lo cual trae como consecuencia, por un lado, a una mayor atención a la propia eficiencia (por un tema de competitividad). Y, por otro lado, a que la optimización de dichos procesos se pueda replicar en otras compañías y, en consecuencia, resulta atractiva para empresas de software tercerizadas.
Esto queda demostrado en las tasas de implementación de soluciones similares en empresas líderes mundiales, entre ellos Tata Steel y Severstal. Donde, una de ellas utilizó tecnologías de IoT industrial y AI para crear un “sistema de recomendaciones” para el operador del horno de arco eléctrico (EAF). Este sistema permitió, sin modificar el equipo de producción, reducir el tiempo de operación en estado energizado durante cada operación de fusión de 55 minutos a 41 minutos, y además satisfaciendo absolutamente de todos los requisitos de calidad (incluido el contenido de FeO en escoria, fósforo y contenido de nitrógeno en el producto a medio terminar). Este “sistema de recomendaciones” asiste al productor de acero dando indicaciones sobre la selección de modos de operación, el recambio del transformador de control del EAF, la operación de los quemadores, y la adición de agentes desoxidantes. Además, el sistema pronostica el tiempo necesario para alcanzar la temperatura exacta del acero fundido en el EAF.
Por supuesto, la operación eficiente de tales sistemas requiere el análisis de los datos históricos específicos de cada horno para la determinación precisa de sus peculiaridades, y para el cálculo de predictores que pronostiquen el tiempo de fusión para una composición y un peso de carga dados.
Dichos sistemas, basados en IoT y AI, están siendo implementados no solo en los procesos de fusión, sino también en otros ciclos de producción. El mayor éxito ha sido registrado en la línea de laminación en caliente, donde el uso de estos sistemas permite reducir la tasa de rechazo, reajustar oportunamente los rodamientos de los laminadores, y asegurar la reasignación de productos. Los laminadores y rodillos están equipados con sensores y un cierto número de etiquetas que garantiza un control completo del estado de cada equipo de laminación. Se relevan datos históricos que se utilizan para determinar los predictores, y combinaciones de etiquetas para pronosticar el estado crítico de una posición individual que causa el rechazo. Con todo esto, el “sistema de recomendaciones” proporciona un pronóstico en línea de las características cualitativas del material rodado y recomienda cambios en la configuración de cada laminador o mesas de rodillos para compensar cualquier consecuencia adversa. El “sistema de recomendaciones” ha permitido reducir la tasa de rechazo en al menos un 0,3% y ha garantizado el mantenimiento oportuno del equipo de la planta.
Beneficio para las empresas
En la metalurgia no ferrosa, soluciones similares a las mencionadas anteriormente recién comienzan a implementarse debido a la complejidad de los procesos de producción, donde la comprensión de muchos aspectos tecnológicos aún tiene un carácter generalizado y descriptivo. Es debido a esto que tradicionalmente las decisiones operativas no son automáticas; es el operador o experto metalúrgico quien toma las decisiones correspondientes basándose en dos aspectos: el procedimiento existente (que tiene un cierto rango) y su propia experiencia (dentro de este rango). La inteligencia artificial (IA) se utiliza cuando las herramientas de automatización tradicionales no han podido desafiar al experto metalúrgico – en soluciones operativas con lógica difusa. Como regla general, estas son decisiones de rutina que los empleados de la empresa deben tomar diariamente o incluso docenas de veces al día.
En su actual grado de desarrollo, la IA aún no es capaz de crear nuevos métodos o soluciones; su función es más bien la de optimizar lo ya existente: por ejemplo, reducir el uso de energía o materiales de consumo, optimizar la operación de los equipos, y controlar de calidad del producto.
Como esto significa la optimización de los procesos de producción establecidos, no se debe esperar la transición a un nivel de eficiencia significativamente alto debido a la implementación de AI: como regla general, el efecto varía de 3% a 10%. Un gran aumento de la eficiencia nos muestra que el proceso inicialmente no había sido configurado de la mejor manera y es probable que los resultados sean integrales. Pero incluso un 3% de optimización de gastos es un indicador financieramente significativo para las empresas grandes y medianas.
Por ejemplo, nuestra experiencia ha demostrado que el uso de modelos AI de optimización para el proceso de flotación, incrementa el factor de extracción en un 3,5% en promedio, y para la electrólisis aumenta la eficiencia en un 4,7%.
Rumbos prometedores
La “visión artificial” es una de las áreas más populares y de más rápido crecimiento del uso de inteligencia artificial en la metalurgia no ferrosa. Y se enfoca en el desarrollo de tecnologías que permitan obtener imágenes de objetos reales, procesarlos, analizarlos y luego utilizar los datos obtenidos para resolver problemas aplicados. Por ejemplo, en caso de querer monitorear una cierta área de producción: rastrear en línea de cátodos y ánodos que se cierran en el taller de electrólisis, reconocer el material en el transportador, y clasificarlo según su calidad.
Las soluciones basadas en esta tecnología ya se han implementado en los equipos electrolíticos operativos de varias empresas del Grupo Rusal. El uso de tecnologías de “visión artificial” en los talleres de electrólisis permite no solo optimizar el proceso de producción y reducir significativamente los costos (incluso debido al consumo eléctrico), sino también mejorar la seguridad de la producción y el cuidado del medio ambiente.
“Digital twin” es un modelo matemático de un proceso de producción. Los operadores de producción pueden usar datos de “Digital twin” para recibir recomendaciones en tiempo real para controlar el proceso de producción. La solución se utiliza para monitorear el consumo de materiales y recursos energéticos, detectar elementos rechazados, así como para monitorear los parámetros del proceso. Así es que, en la compañía Kola Mining & Metallurgical, el “Digital twin” asegura la optimización del acabado de mate desde los hornos de fusión hasta los convertidores.
Las tendencias del mercado
Según la investigación realizada por la consultora Stratistics MRC, se prevé un consumo mundial creciente de metales no ferrosos a largo plazo (Crecimiento del consumo de cobre en 1,7 veces, aluminio – 1,5 veces, zinc – en 1,7 veces hasta 2030) debido a:
– creciente consumo en los sectores tradicionales (que satisfacen las necesidades de la creciente población y de la urbanización)
– creciente demanda en sectores de nueva economía (fuentes de energía renovable, nuevos transportes)
– dificultades de sustitución con productos alternativos (excepto el plomo).
Según lo previsto por International Copper Study Group, los resultados de 2018 muestran un déficit de cobre en el mercado global que supera las 90 mil toneladas. En 2019 se espera que disminuya a 65 mil toneladas. Sin embargo, el déficit en 2020–2022 puede aumentar nuevamente a 200–250 mil toneladas, debido a que las viejas minas se están agotando, el contenido de cobre en sus minerales está disminuyendo, y que pocas nuevas instalaciones a gran escala se pondrán en servicio (exceptuando las rusas, solo existe Cobre Panamá en Panamá y Mina Justa en Perú). Todo esto conducirá a un aumento del costo de producción de cobre y del precio del metal.
Se prevé que el consumo de aluminio para la fabricación de un automóvil aumentará, en promedio, del nivel actual de 100-120 kg a unos 250 kg en 2025, lo cual creará una necesidad adicional de 12 a 16 millones de toneladas de aluminio al año para el 2025, y entre 27 y 35 millones para el 2050.
Por otra parte, los impulsores para el crecimiento del consumo de zinc serán la industria del acero (revestimiento galvanizado con zinc), producción de latón y bronce. La creciente producción de un nuevo tipo de vehículos motorizados creará una demanda adicional de zinc igual a 2,4 millones de toneladas al año para el 2030, y unos 3,6 millones de toneladas para el 2050.
Es decir que, factores importantes previstos en la metalurgia no ferrosa serán, el endurecimiento de los requisitos para la producción amigable con el medio ambiente, y el aumento de la eficiencia energética y productividad laboral. Por lo tanto, la demanda de soluciones digitales en la producción en metalurgia no ferrosa, particularmente referidas a un aumento de la eficiencia, crecerá inevitablemente.
Artículo de colaboración:
KONSTANTIN GORBACH
Director del departamento de aplicaciones intelectuales
Zyfra Company